|
BG&E is renowned for its technical excellence, ability to look at things differently
and work seamlessly in locations around the globe.
BG&E recently completed its 40th year of providing innovative and elegant solutions
that transform challenging projects into outstanding successes.
It is with pleasure that we invite you to join us in the journey of the next forty
years.
Welcome to the Roaring Forties!
|
|
|
|
BG&E recently welcomed 180 distinguished guests to join in celebration, marking
our 40th year of innovation and outstanding engineering excellence. Gathering in
the imposing foyer of Central Park, Perth CBD, our valued clients and associates
enjoyed an evening of networking and celebration. We thank you for making the evening
a success. Photos can be found
here.
40 year celebrations will continue in Sydney and Brisbane over the next few months.
|
We received excellent feedback regarding the evening. From all accounts, it seemed
attendees enjoyed the opportunity to network and relax with colleagues and clients.
The team worked hard behind the scenes to create the evening and we are appreciative
of the feedback we received. A few comments are paraphrased below.
Lou Cotter,
Director, the Buchan Group— ‘Chris and I would like to thank you
for the opportunity to celebrate the 40+ years of successful operation and growth
of your Engineering practice with you and your team last night. It was a very good
turnout, which is testament to your loyal client base!’
Ian Smith,
Principal, Golder Associates Pty Ltd— ‘Congratulations on your
40th and thank you for a great night. You must be very proud of what you have achieved
and your strong foundation for further success. The attendance last night was a
testament to the esteem in which BG&E is held in Perth. I felt honoured to be
invited and appreciated the opportunity to catch up with so many friends at BG&E
and in the industry. We recognise that being able to work with BG&E over the
years has been a major contributor to our success in WA. Best wishes for the future.’
Andrew Bland,
Business Development Manager, Georgiou— ‘Thank you for an entertaining
evening last night, it was good to mingle with construction industry friends…it
was good to catch up with members of the BG&E team. I know how difficult it
is to organise and coordinate these events and everything appeared to go like clockwork.
I think John Flecker’s summary of the 40 year history of BG&E as “Bloody Good
Engineering” hit the nail on the head – we look forward to the next 40 years! Once
again thank you for a great evening and the anniversary book.’
|
|
|
|
BG&E designs concrete LNG storage tanks, a task that requires sophisticated
finite element analysis and the consideration of unusual and extreme scenarios.
LNG storage tanks are designed to international standards and require multiple levels
of redundancy to maximise safety.
While not a new concept, ‘Membrane Containment’ type systems are just beginning
to develop popularity for the above ground storage of LNG.
Modern membrane systems originated from the containment systems used in large LNG
carriers. They consist of a thin, flexible, stainless steel ‘primary’ membrane supported
by thermal insulation panels. These insulation panels are, in turn, attached to
a load bearing and vapour tight support. In this case, a large, concrete outer tank
with an applied, polymeric vapour barrier provides this support, carrying the product
load.
In a membrane containment system, the functions of product containment, insulation
and structural support are separated in the most efficient way.
While the mechanical components and the membrane system are typically proprietary
components supplied by a membrane supplier, the outer concrete tank is adapted specifically
for each project. Opportunities arise by considering the client's design criteria,
the contractor's preferred construction methodology and specific site conditions.
The outer concrete tank consists of a post-tensioned concrete wall, which is supported
by and monolithically connected to, a reinforced concrete base slab with thickened
edges. Typically, a reinforced concrete dome roof is also provided, cast over a
steel membrane plate. The roof is required to take the weight of the pump wells
(which are hung from the roof), as well as provide support for external platforms,
pipework and a suspended deck inside the tank.
Design of the outer concrete tank is complicated by its shape and monolithic nature,
as well as various construction stages such as the roof construction, provision
of temporary openings and hydrotesting. One of the critical loading scenarios is
the accidental/abnormal case of leakage of the primary containment. For this design
scenario, it is considered that the LNG has bypassed the primary membrane and acts
directly on the tank wall (or secondary barrier, where present), creating significant,
thermally induced stresses and changes in material properties with cryogenic temperatures.
BG&E overcomes such design challenges, using sophisticated modelling and analysis
procedures.
The weight of more than 80,000 tonnes of stored LNG is significant, so it is critical
that the foundation is able to resist the load. Different foundation options are
possible - such as piled foundations or spread foundations - with or without various
soil improvement techniques.
See Figure 1 below for a more detailed explanation of the components of a ‘Membrane
Containment’ type tank.
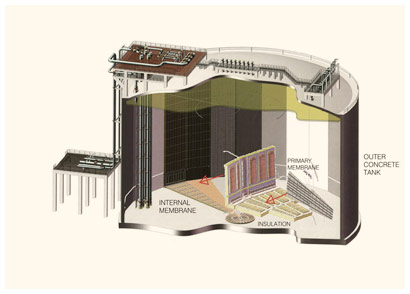
Typical membrane type LNG
storage tank (courtesy of GTT)
BG&E has been designing a ‘Membrane Containment’ type LNG tank for Laing O’Rourke
as part of the LNG Limited Fisherman’s Landing project in Gladstone, Queensland.
The proposed, above ground tank has a net capacity of 180,000m3 and has
a monolithic, reinforced concrete roof. LNG Limited together with Laing O’Rourke
evaluated various tank designs specifically for the Australian industry and selected
the membrane tank due to its advantages of shorter construction durations and reduced
costs.
LNG Limited’s core objective for this project is to commence first LNG production
in 2014. If that timeframe is achieved, the Gladstone LNG tank will be the first
membrane type LNG tank in Australia.
|
Natural gas is an important part of today’s world energy sources. Its popularity
is increasing due to its comparatively low carbon footprint (per unit of energy
produced) and ability to be stored, transported and piped to homes. By processing
and refrigerating natural gas, it can be turned into Liquefied Natural Gas (LNG)
– a liquid product which is around 1/600th of the volume of natural gas
in its gaseous state. Countries with an energy deficit, (such as Korea and Japan)
can import LNG from locations with an energy surplus.
In order to transport the LNG, it must be stored at exportation and importation
facilities in large, insulated tanks before and after shipping. Many LNG storage
tanks can hold nearly 200,000m3 of LNG – the equivalent of 80 Olympic
size swimming pools of cryogenic product.
|
Above ground LNG storage tanks are the most common way of storing cryogenic Liquefied
Natural Gas (LNG) due to their practicality and cost.
|
Advantages of above ground ‘Membrane Containment’ type tanks:
|
Typically a shorter construction programme than ‘Full Containment’ tanks
|
|
|
Can be more economical than ‘Full Containment’ type tanks (with a 9% Nickel alloy
inner tank)
|
|
Membrane type containment tanks are prevalent in the LNG import terminals of Japan
and South Korea – but most of them are built below ground.
|
|
|

BG&E is happy to announce our newly refurbished website, where you can find out
more about our projects, services and capabilities.
As part of our efforts to bring interesting industry information to as many people
as possible, we have added social media tools, Facebook and Twitter, to our range
of communication channels. These tools help us to be more connected with clients,
engineering students and anyone interested in staying in touch!
Join
in the conversation at our Facebook page: facebook.com/BGEengineering
Why
not follow us on Twitter: twitter.com/#!/bgeeng
|
|
|
What is it? Building information modelling
(BIM) is a design method whereby software is utilised to generate complex, 3D representations
which contain intelligent information about the building components. This is useful
to all parties involved throughout the life of the building, including designers, quantity
surveyors, builders, clients and facilities managers.
Model element attributes and other material properties embedded in the structural models, can be effectively coordinated and integrated with architectural and building services models.
BG&E is proficient in the use of Building Information Modelling within the Structural
engineering industry.
Consider the use of BIM for your design projects: see 'How
to get started' on our BIM page for more information about when BIM is applicable.
BG&E are utilising other 3 dimensional modelling software with Tekla Structures for structural
documentation and fabrication shop drawings.
|
BG&E utilises a number of CAD software packages across the business. In 2008,
we adopted Autodesk® Revit® Structure to complement our existing modelling
and drafting capabilities and also soon after commenced utilisation of Tekla Structures.
We have used a gradual integration of Revit modelling and documentation into our
project delivery.
The majority of all our building documentation across BG&E in the past
3 years, has been prepared using Revit. We apply it in particular where required by the client and where we consider
that modelling would expedite and enhance the delivery and construction process.
For several of these projects, BG&E have been the only member of the design
team using Revit modelling.
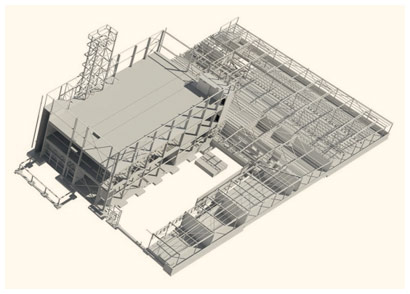
Fiona Stanley
Hospital, Central Energy Plant, Perth, WA
BG&E have documented over 100 projects using Revit® Structure. Many of these
included Design and Construct of multiple buildings. An example is the Fiona Stanley
Hospital, where we modelled 5 buildings and a buried service tunnel using Revit®
Structure. Currently, BG&E is providing the structural engineering modelling
for hospital, residential, commercial, civic building projects as well as for civil
coordination. For some of these projects, like the QEII Central Energy Plant buildings the project
design team is responsible for delivering level 6D models.
|
NCIG Wharf, Newcastle |
City of Lights, UAE |
Nebo Project, Queensland |
|
|
|
The Curtin University Engineering Pavilion was designed with a 5 ‘Green Star’ rating
in mind.
BG&E researched a number of cutting edge material technologies for use in the
structure of the building, as part of this drive to obtain a 5 star rating.
The building design was chosen to explicitly show its engineering aspects. A steel
diagrid structure has been chosen as part of this expressive concept. This shares
the wind loads on the triple height atrium glazing across multiple members and acts
as the primary stability bracing system for the building. Combining the atrium wall
support system with the bracing system in this way has removed some structural shear
wall elements from the design.
The diagrid that wraps around three sides of the atrium at the west end of the building,
is a fully welded, exoskeletal frame, fabricated from 300 x 200mm, rectangular hollow
sections. These were prefabricated in the shop into sections of both the cladding
and frame, up to 20 x 6m in size. These giant assemblies were then manoeuvred onto
site, erected using a 200t crane and site welded together in position with a prepped
site butt weld, to give a continuous diagrid look.
Reuse Recycle Reduce
A triple height atrium provides connectivity to the three floors of the building,
containing walkways and vertical circulation. One of the walkways was an existing,
1970s concrete link at first floor level. This previously joined the buildings either
side of the site. A collaborative and extensive design effort between the architect,
Taylor Robinson and BG&E, meant that this walkway was incorporated into the new
atrium, reducing demolition and new build requirements.
The floor slabs are post-tensioned to reduce the volume of concrete used and maximise
space for services in the ceiling, without the need to increase the building height,
which would have added to the material use in facades and walls. This additional
services space safeguards the building for the future demands and changes of the
university.
Cement Substitutes
All concrete across the project contains Portland cement replacement materials in
the concrete mix design. The replacement product used was ground granulated blast
furnace slag (GGBS), which comes from the steel making industry as a by-product.
Every tonne of Portland cement produced, represents one tonne of CO2 released into
the atmosphere, so using a by-product instead of manufactured cement is beneficial
to the environment. Typically, a minimum of 15-30% replacement was used in mixes,
depending on the type of element.
The Roof Solution
The solution for the support of the roof structure across the 19 x 17m exhibition
space was to use three, bow string trusses supporting timber purlins. The bow string
trusses are comprised of two, 115 x 460mm glulam timber beams, either side of a
6mm thick, steel flitch plate as the top chord of the truss and a 25mm diameter,
tensioned stainless steel rod as the bow string bottom chord. Combining the materials
kept the use of steel to a minimum, without the need for excessively large timber
members. All timber was specified as being Forest Stewardship Council certified.
|
BG&E is known for its ability to create innovative solutions that increase the green
rating for structures. For more information about our capabilities in Sustainability,
visit our website page here.
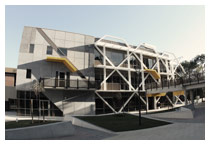
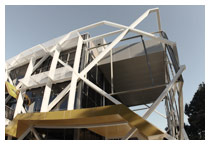
|
|
|
We have an international reputation for engineering excellence and our projects have won numerous awards. This year we have received the following awards:
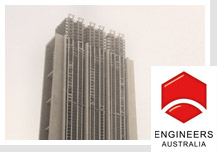
|
Index Building,
Dubai, UAE— Engineers Australia Sydney Division, 2011 Building
& Structures Excellence Award
|
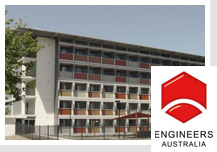
|
Australian National
University Student Accommodation, Canberra, ACT— Engineers
Australia Sydney Division, 2011 Finalist Products, Manufacturing Facilities & Process
|
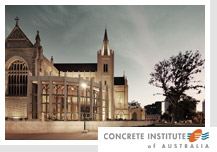
|
St Mary’s Cathedral,
Perth— Concrete Institute WA, 2011 Awards for Excellence in Building
Category
|
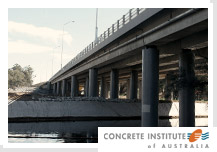
|
Swan River Bridge
on Reid Highway, Perth— Concrete Institute WA, 2011 Highly
Commended in the Engineering Project Category (shared with Golder Associates)
|
|

We would love to hear from you! If you have any feedback, comments, questions or
just want to get in touch – please email us on info@bgeeng.com.
We look forward to your company in our next issue of The Roaring Forties.
|
|